QS Motor Specification (e.g. 3000W 205 50H V3 Electric Bike Spoke Hub Motor)
1.Motor Type: BLDC Outer Rotor In-Wheel Hub Motor With Hall Sensor
2.Brand: QS Motor,QSMOTOR
3.Motor Design: Double axle with 205mm diameter hub motor, 36 spoke holes, OD 4.2mm
4.Suitable Rim size: 24inch, 26inch E-Bike Wheel, 17inch, 18inch, 19inch moped wheel.
5.Magnet Height: 50mm, 16 pole pairs
6.Stator: Aluminmum Core
7.Rated Power: 3000W (could be 12kW peak),
8.Speed(customizable, depends on wheel size):
48v 21km/h~65km/h
60v 26km/h~80km/h
72v 32km/h~80km/h
9.Max Torque approix 182N.m
10.Thermic Probe: KTY83/122 (as default)
11.Max Efficiency above 86%
12.Brake type: Disc brake, PCD6*44mm
13.Drop-outs: 150mm~154mm
14.Dual Hall Set with water proof connectos
15.10mm² Phase Wire (not include insulation)
16.Waterproof Grade: IP54
17.Color: Black (as default)
Gross Weight 14.5kg (with freewheel)
Package: 34cmX34cmX33cm
PS. Temp Sensor Options: KTY84/130, KTY83/122, 10K@25C NTC(model MF58-103F3950).
QS Motor could work 120 ℃ in half an hour without damage.
Suggestion (Setting of Controller)
When it’s 130 ℃ inside of motor (in 30s), the current should be limited 50%.
When it’s 150 ℃, the controller shut down. When it drop down to 110℃, the controller work again.
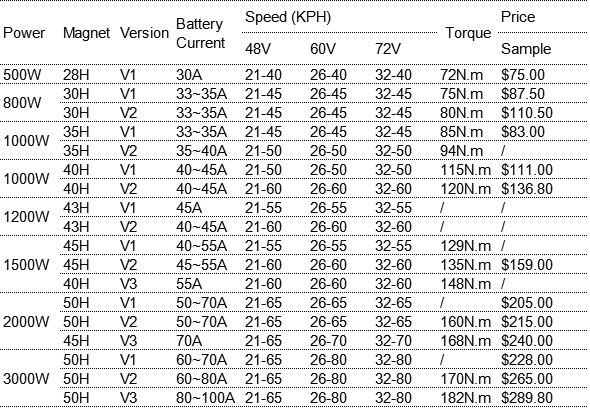
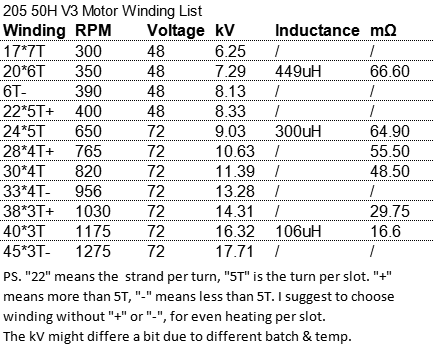
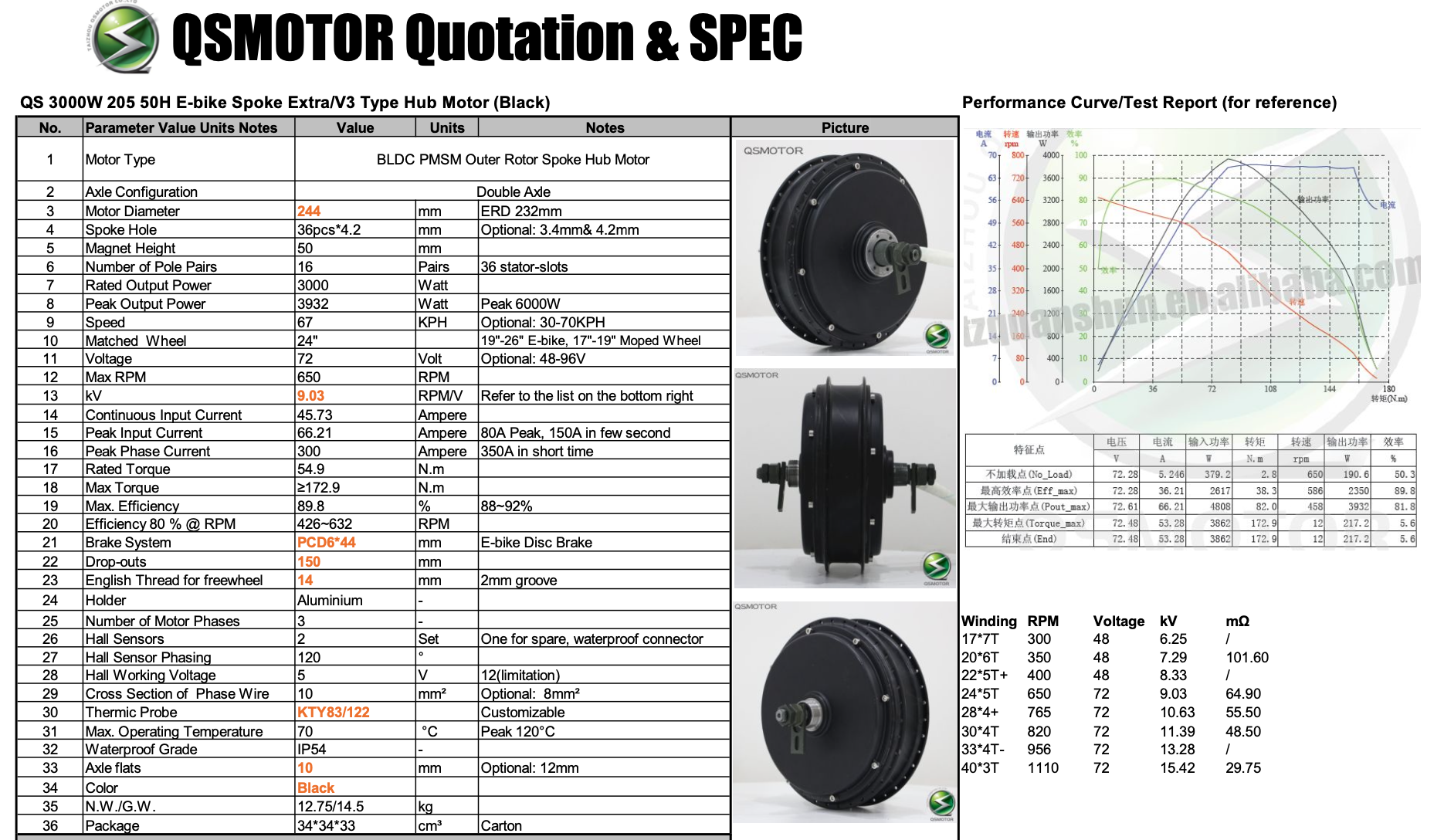
Phase amps recommendations and info
strand cross section – 0,2mm²
Phase cross section inside motor
5T 24×0,2= 4,8 mm²
4T 30×0.2= 6.0 mm²
“For QS 3000W 205 50H V3 Spoke Hub Motor, 24X5T Winding.
QSMotor on max phase.
Phase current, we suggest to set 200A (10s), 220-240A (1-2s).
For battery current, it could be 150A (72V).
For other winding motor, we suggest to set max phase current 40 Time of Wire cross-sectional area (10s).
E.g. 24X5T winding, the wire cross-sectional area is 24X0.204=4.896mm²
Peak Phase Current 4.896*40=195.84A.”
QS Motor V1/V2/V3 Type Motor
There are three types, Normal/V1 type (low cost), Export/V2 type (Cost-effective) and Extra/V3 type (Best Performance).
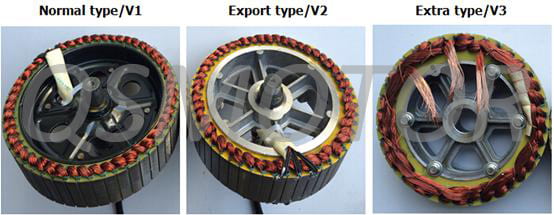
1. Difference between V1 & V2
Holder: Iron(V1), Aluminum (V2)
Hall: One hall with Normal connector(V1), Two halls with Waterproof connector(V2)
Stator: V2 have a stronger configuration, more cooper, thicker section surface, energy saving in usage.
Magnetic Steel Grade: V2 ≥ V1
Efficiency: 84~87%(V1) 86~88%(V2)
In short, normal type is standard configuration, while export type is high configuration.The price differs because of the cost of raw materials.
2. Difference between V2 & V3
The raw materials are alike, main difference in inner construction.
For V3 (16 Pole Pairs): stronger configuration than V2, wider lamination,
more cooper wire /thicker Cross-sectional area section, bear more current
in usage. Higher torque at same current, lower temperature rise, more stable in high current.
Magentic Steel: V3 is wider and thicker.
Efficiency: 86~88%(V2) 88~92%(V3); Thus, V3 have best performance.
PS. for the same V1 steel/iron stator motors, QS Motor performance better on lifetime & stability becasue of good raw material. So the cost is more than normal hub motor in the market.
E.g. 1. Choose C&U bearing which is motorcycle standard, more quiet when riding.
2. High Coil space factor, better efficiency.
3. Silicon steel sheet 0.35mm instead of 0.5mm, less current consumption & low temp rise.
4. Insulation varnish outside of varnished wire, max 180 ℃ than normal 120 ℃.
5. Better magnet, demagnetizing less than 1% than normal 3%.
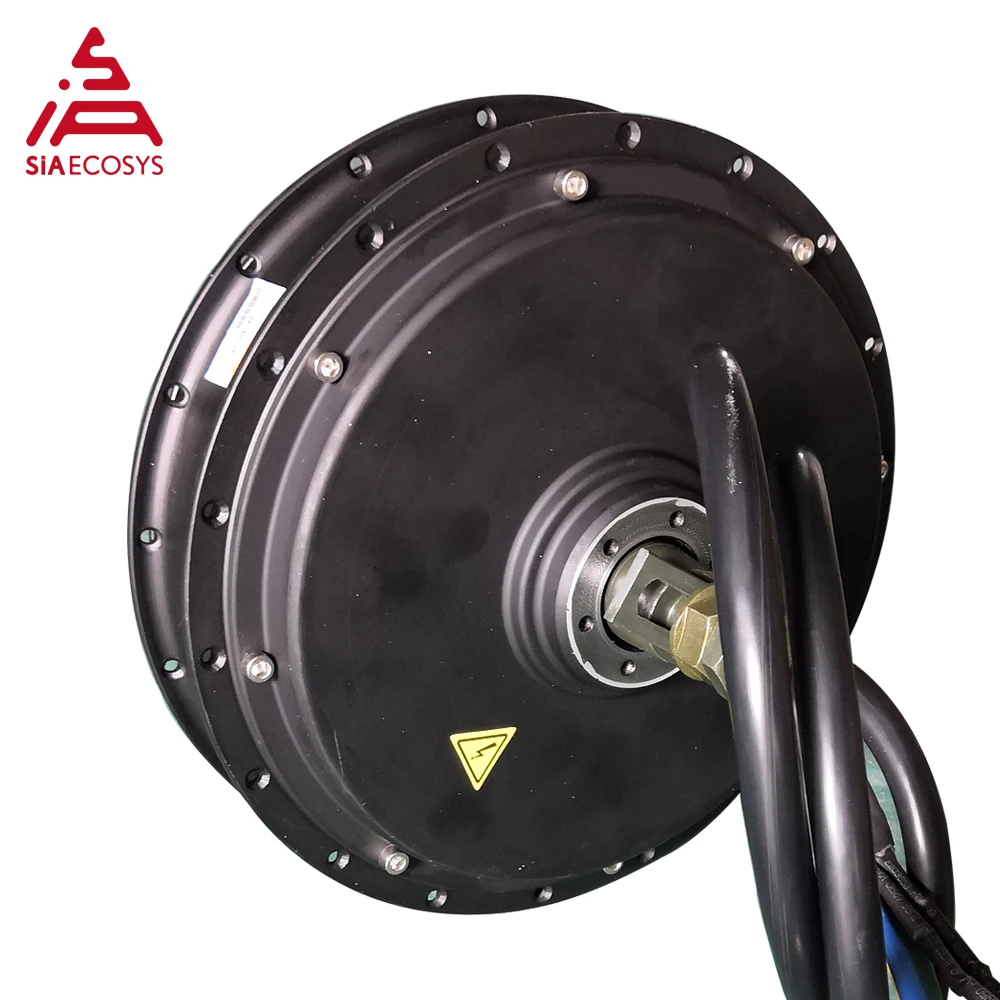