Plastic and rubber materials have many useful physical and mechanical properties, but it can be challenging to select the right material for a specific project. Shore hardness is an excellent measurement to help you determine material suitability.
Shore hardness measures the hardness of a material by determining its resistance to indentation. These resistance values can be found using a durometer, which measures the hardness of plastics, silicone, rubber, and other polymers and elastomers on a standardized scale to ensure that the material has the right amount of flexibility or hardness.
As a leading developer and manufacturer of liquid molding technology, Hapco has the in-depth knowledge and expertise to help you determine the perfect material for your application. With more than 50 years of experience, our ISO 9001 certified organization is dedicated to providing quality urethane and epoxy materials to meet your needs. We use the durometer hardness scale—also known as the Shore hardness scale—to help you determine the best molding materials for your project.
Shore Hardness Scale
The Shore hardness scale is an internationally accepted standard that quantifies the hardness of a material. It offers a comprehensive snapshot that makes it one of the most valuable plastics and rubber hardness scales available. The scale operates within a numeric range of 00 to 100, with 00 being the softest material and 100 being the hardest.
To measure different categories of materials, there are three main Shore hardness scales:
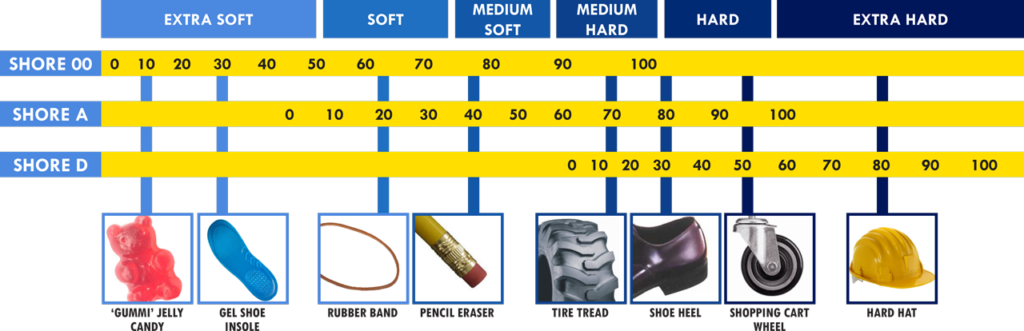
- Shore 00 is typically used for soft and flexible materials such as gels, soft foams, and highly flexible rubbers.
- Shore A measures flexible mold rubber materials. This range includes most rubbers from extremely soft and flexible up to hard rubbers with minimal flexibility. It also evaluates non-rubber plastics that are semi-rigid and somewhat flexible.
- Shore D is reserved for testing hard and semi-rigid plastics and rubbers.
Shore Hardness Comparisons
Shore hardness scales offer easily quantified hardness levels. To illustrate, we can compare common objects and materials that exhibit similar hardness. Use the durometer chart below to help you narrow down your shore hardness requirements.
Shore 00
- Marshmallow: 10 Shore 00
- Gel Insole: 30 Shore 00
Shore A
- Rubber Band: 20 Shore A
- Mouse Pad: 30 Shore A
- Inner Tube: 40 Shore A
- Pencil Eraser: 50 Shore A
- Tire Tread: 60 Shore A
- Shoe Sole: 70 Shore A
- Leather Belt: 80 Shore A
- Phone Cord: 90 Shore A
Shore D
- Textbook Cover: 40 Shore D
- Golf Ball: 50 Shore D
- Shopping Cart Wheel: 60 Shore D
- Wooden Ruler: 70 Shore D
- Computer Case: 80 Shore D
- Bone: 90 Shore D
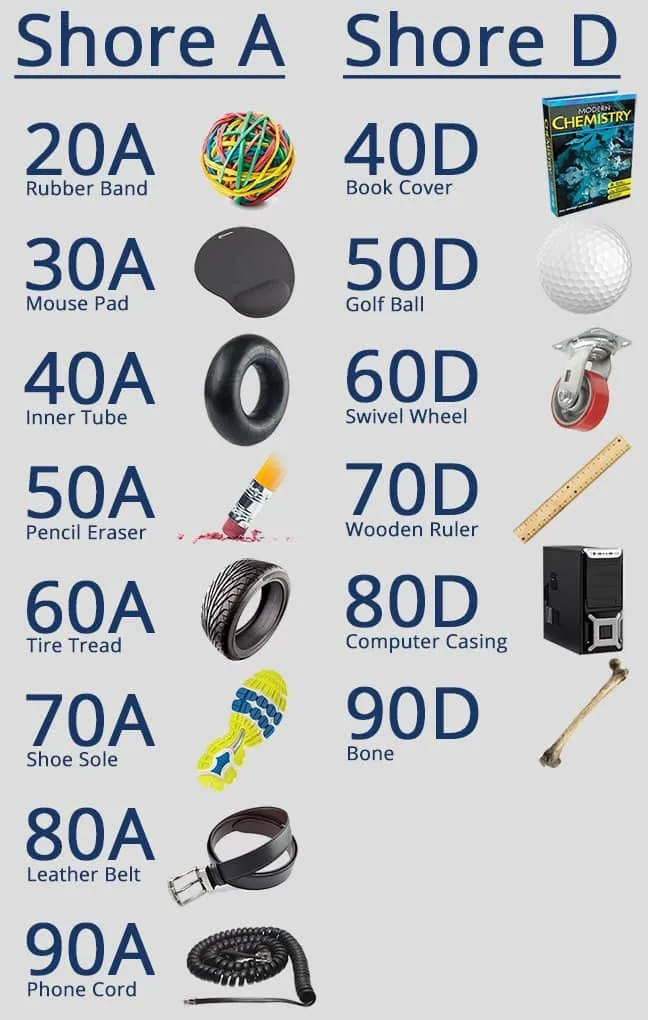
There are different Shore Hardness scales for measuring the hardness of different materials. These scales were invented so that people can discuss these materials and have a common point of reference. As you can see from the chart below, there is overlap on the different scales. For example a material with a Shore hardness of 95A is also a Shore 45D.
The Shore 00 Hardness Scale measures rubbers and gels that are very soft.
The Shore A Hardness Scale measures the hardness of flexible mold rubbers that range in hardness from very soft and flexible, to medium and somewhat flexible, to hard with almost no flexibility at all. Semi-rigid plastics can also be measured on the high end of the Shore A Scale.
The Shore D Hardness Scale measures the hardness of hard rubbers, semi-rigid plastics and hard plastics.
How Do You Physically Measure A Material’s Hardness?
The different Shore Hardness scales measure the resistance of a material to indentation. A ‘Shore Hardness’ gauge (looks like a round tire pressure gauge) has a needle on a spring protruding from one end. The needle is placed against the rubber or plastic and pressure is applied.
Once the gauge is pressed firmly against the material and the needle has penetrated as far as it can go, the measurement needle will indicate the corresponding hardness measurement.
What Shore Hardness means to you as a mold maker:
Shore Hardness becomes an important factor when considering which mold rubber you should choose for your for making a mold of your original.
The consideration is “how easily will you be able to extract your original model (and subsequent castings) from the rubber mold once it is cured“.
For example, you would not choose a rubber with a durometer of 70A to make a mold of a plaster standing ballerina with thin, protruding arms bent at opposing angles. A 70A rubber (as hard as a car tire) is stiff and would not offer enough flexibility to extract this model without breaking it.
A better choice would be a Shore 30A rubber or softer that would offer enough flexibility to easily extract the model.
Under what circumstances would you use a Shore 70A rubber? A common application we encounter from the world of concrete casting would be making molds of flat original models (paving stones, for example). This model configuration does not require much flex from the rubber mold to extract the original or subsequent castings. Using a 70A urethane rubber also gives you tremendous abrasion resistance and therefore the longest mold life for this application.
Sources:
https://hapcoincorporated.com/resources/hardness-chart/
https://www.smooth-on.com/page/durometer-shore-hardness-scale