So, how do you know what size wires to use for your battery project? It can be confusing, but it can also be dangerous. If you don’t use a large enough wire, the wires will become excessively hot under the intended load. And while we do recommend over-sizing wires, if you oversize by too much your build will be more expensive than necessary.
Tables and Charts For Proper Cable and Wire Sizes
Most people don’t realize that the amount of current a given wire can carry is dependent on the type of insulation it has. That’s right, the same amount of copper can carry more current if its insulator is rated for higher temperatures.
For example, Non-UF-B (Metallic Sheathed Cable) can only carry 15 amps at 14 gauge because of the type of insulator used. In contrast, THHN and XHHW-2 insulators have high heat resistance, enabling 14 gauge cable to comfortably carry 25 amps.
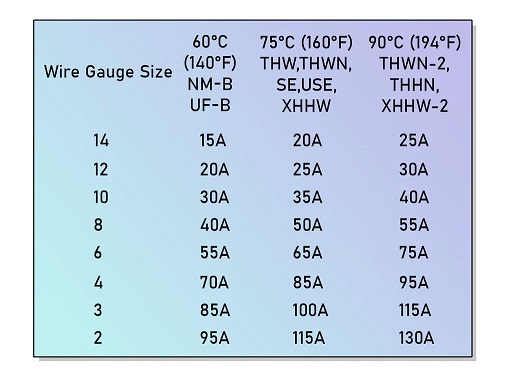
You can use the table above for sizing the wire for the charge and discharge connectors for your battery pack. All you have to do is cross-reference the type of wire you want to use with your battery’s peak current.
It’s important to not run anything at its limit, so, whatever the highest current discharge your BMS supports, use wire that has about 20% extra current carrying capacity.
Wires used internally in the battery pack construction are relatively short, so ampacity is all that matters. You don’t really have to worry about voltage drop so much at these lengths.
What is Voltage Drop In Wires
You might assume that cables transfer power without consuming it, but in practical application, all wires and cables have some amount of resistance and therefore use some amount of power.
This resistance of a given conductor is directly proportional to its length but inversely proportional to the conductor’s diameter. This means as a given wire’s length increases, its resistance increases. It also means that larger gauge wires will have lower resistance.
Due to this unavoidable, intrinsic resistance, a voltage drop occurs when current flows through any conductor. When working on small scales or with low-power projects, this voltage drop is negligible. If you are, however, building a larger system, or something that consumes a high amount of current, then these small drops can add up to big power losses.
The amount of voltage drop between your battery and your load can result in a significant loss of power and battery life.
How To Determine The Proper Cable and Wire Size For a Given Load?
When it comes to determining the correct cable and wire size, you must take several factors into consideration. One of which is circuit load. If all else is equal, the smaller the load the smaller wires you need.
Making sure you have the right wire size for your DC electrical project is crucial. Remember, if a wire is too small it will heat up and could eventually ignite. Something as simple as using the right fuse can reduce the chances of a fire to nearly zero.
Make sure to avoid solid wire. This may seem counter-intuitive, but stranded wire is usually the best option. Solid wire is stiff and hard to bend compared to stranded wire. It’s also a lot harder to solder. Also, their added stiffness makes solid wire very difficult to splice compared to stranded wire.
Universal Wire Sizing Chart
This chart effectively replaces several pages of sizing charts. This can be applied to literally any working voltage, at the acceptable voltage drop of your choosing. This chart will work for any voltage and voltage drop and works with AWG and metric sizing.
VDI stands for Voltage Drop Index and is a reference number based on a wire’s total resistance.
You can find your VDI by performing the following calculation:

When doing this calculation, make sure to only consider the one-way distance between the battery and the load. For the %VOLT DROP, choose your acceptable voltage drop percentage.
Consider this example:


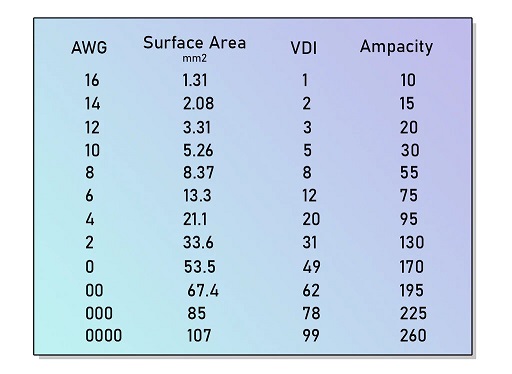

You can also simply multiply your calculated VDI by 1.1 to find out what size metric cable you need for your project.
NOTE: Metric standard wire sizes are available in 1, 1.5, 2.5, 4, 6, 10, 16, 25, 35, 50, 70, 95, and 120 mm².
It’s important to keep in mind that while this calculation does tell you what size cable you need to maintain a certain voltage at a certain current, it does not account for the ampacity of the cable itself. So, for best results in determining cable size, the VDI and ampacity ratings should be compared and the larger cable of the two should be chosen.
Source/Author: https://cellsaviors.com/blog/how-to-size-wire-fuses-and-nickel-strip-for-a-lithium-battery-pack